In the complex world of haulage and logistics, one often overlooked factor can significantly impact vehicle performance, tyre longevity, and fuel efficiency: tyre pressure. Gary Lane, Fleet Development Engineer at Prometeon Tyre Group, reveals a critical issue that’s costing fleet operators thousands of pounds in unnecessary wear and potential damage – over-inflation
The hidden cost of over-inflated tyres: a silent performance killer
The ‘inflation inflation’ problem
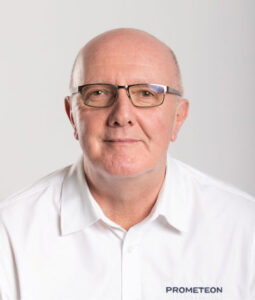
While the focus is often on under-inflation, over-inflation presents an equally significant challenge. “People don’t think to check, or sometimes it just gets forgotten,” Lane observes. Yet, the consequences can be substantial – in terms of vehicle performance, driver comfort, and operational costs.
“At the end of the day, a tyre is like an envelope. It needs the correct pressure to perform,” Lane explains. However, even brand-new vehicles are experiencing a systemic over-inflation problem that begins long before they reach the end-user.
The issue starts during tyre production and transportation. Manufacturers typically inflate tyres to maximum pressures – around 130 psi – during the manufacturing process. “These will be done on fitting machines,” Lane describes, “where they might have 1,000 wheels to build up with tyres from various manufacturers.” The production line inflates to the maximum possible pressure, ostensibly to ensure safety during transport and initial fitting.
However, dealerships often fail to adjust these pressures, a problem Lane has witnessed firsthand. “I was at a customer’s site recently for a tyre inspection,” he recalls, “and they had a brand new tractor unit. On the drive axle, the tyres should have be 90 psi, but they were inflated to 130psi, which is far too hard.”
The consequences of over-inflation
The impact of over-inflated tyres is both immediate and long-lasting:
- Uneven wear: Tyres become bald in the middle while maintaining tread on the outside shoulders. “You’ll have good tread on the outside but in the middle, they’ll be bald,” Lane explains.
- Increased vulnerability: Over-inflated tyres become less flexible, making them more susceptible to damage. “If the tyres can’t flex it can lead to chipping and tearing of the tread.”
- Performance issues: Drivers experience significant discomfort. “The drivers will feel it through their arms, it can feel quite severe when driving on overinflated tyres as the ‘hardness’ ripples up through your arms,” Lane explains, highlighting the physical impact of incorrect tyre inflation.
The financial toll
One fleet operator Lane spoke to experienced substantial financial losses due to this issue. “He’d lost roughly around about £1,800 per truck,” Lane reveals, “due to rapid and uneven tyre wear caused by over-inflation.”
A changing landscape
The good news is that since 6 July 2024, all new trucks have to be equipped with tyre pressure monitoring systems. Lane is enthusiastic about this development, saying it will put the onus on maintenance providers to ensure the correct pressures.
Practical advice for fleet operators
- Regular checks: Don’t assume new vehicles have correct tyre pressures.
- Proper inflation: Understand the recommended PSI for different axles and tyre types.
- Consider specialist inspection: Invest in professional tyre pressure checks.
The impact of tyre construction on fuel efficiency
When it comes to fuel efficiency, tyre construction is an important but often misunderstood factor. While many associate fuel savings with the rubber compound or tread design, Lane explains that the impact of tyre construction is less direct. “The key element in improving fuel efficiency through tyre construction is rolling resistance. The less rolling resistance a tyre generates, the less energy it requires to maintain motion, ultimately reducing fuel consumption,” Lane explains.
The structure of the tyre, particularly the belts inside, provides essential strength to the tread. These belts help the tyre withstand the forces of the road while maintaining performance. However, the most significant contributor to fuel efficiency is the tyre’s tread pattern. “A progressive tread pattern with fewer aggressive features helps reduce rolling resistance,” says Lane. “Tyres designed with low rolling resistance are ideal for fuel efficiency, but they may come with trade-offs in durability, which is an important consideration for fleet operators.”
Tread depth: finding the sweet spot
The depth of the tyre tread plays a crucial role in both fuel efficiency and tyre longevity. Lane notes that while deeper treads can offer better traction, they also increase rolling resistance, which impacts fuel consumption. “For optimal fuel efficiency, the best performing tyres tend to have a tread depth between 3mm and 6mm. This offers a good balance between reduced rolling resistance and durability,” says Lane.
Prometeon’s RO2 Pro Fuel tyres, designed for both steer and drive positions, embody this balance. “The RO2 Pro Fuel tyres are a great example of how careful design can reduce fuel consumption while maintaining a reliable lifespan and performance. They are designed with lower rolling resistance without compromising on wet grip and overall safety,” adds Lane.
Conclusion
Tyres play a pivotal role in improving fuel efficiency for commercial fleets, and the decisions made in tyre selection and maintenance can have significant financial and environmental implications. From choosing the right tread design and maintaining optimal tyre pressure to considering retreading as a sustainable alternative, fleet operators have several ways to enhance fuel economy while ensuring safety and durability.
As Lane highlights; “The key to fuel efficiency is understanding the balance between energy-saving features and the practical demands of a fleet. By focusing on the right tyre construction, maintaining proper pressure, and considering retreading, fleets can optimise fuel use without compromising on performance.”